Powder Coating
What is Powder Coating?
Powder coating is a method of applying a protective and decorative layer to metal surfaces. Unlike liquid paints, it is applied in a dry powder form. This powder is also called powder coating paint.
It’s not possible to use this paint at home when you renovate your bedroom. But for manufacturing tasks, powder coating is the most modern and high-performance solution.
Powder Coating Overview
- Thermoset powders undergo chemical cross-linking during curing, resulting in a stable, heat-resistant coating.
- Thermoplastic powders melt and flow when heated but do not undergo chemical changes. This results in a coating that is resistant to scratches, abrasion, and fading.
Technology Advantages
Why Choose Powder Coating?
Powder coating offers significant advantages for various industries, thanks to its performance, environmental benefits, and economic efficiency.
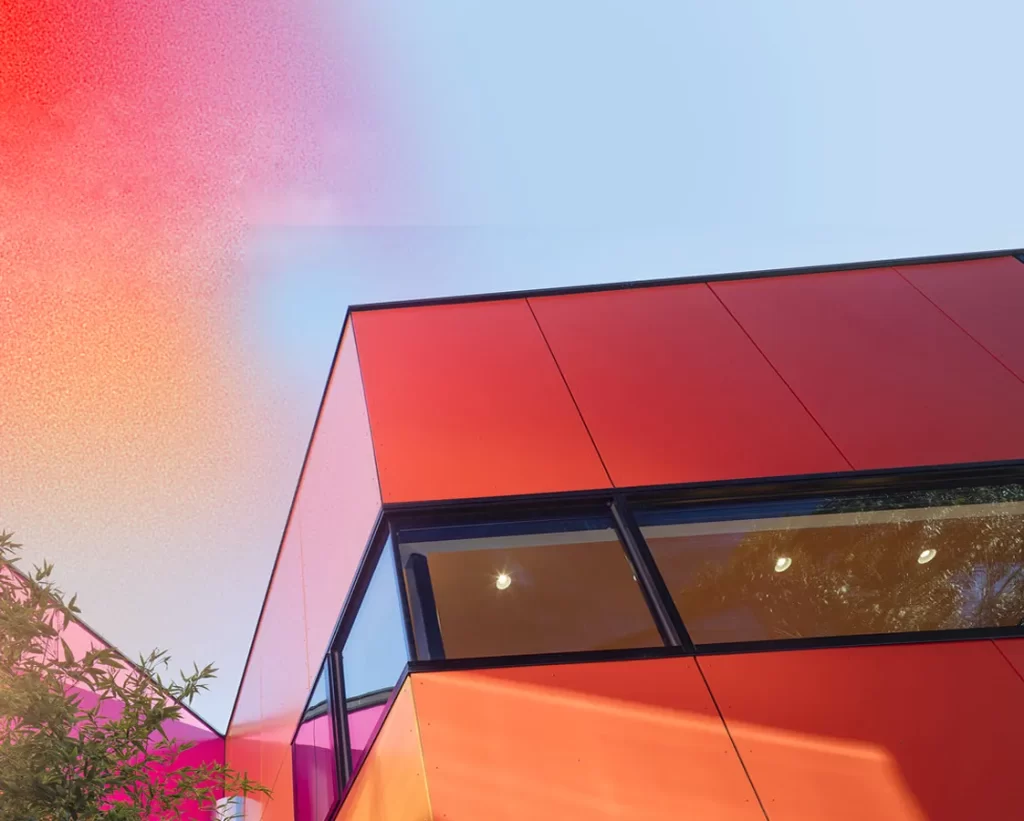
Durability from 12 months to 30 years
- Surface Protection: When melted, the powder forms a durable film that is more resistant to damage compared to liquid paints. The surface is highly resistant to chipping and scratching.
- Long-Lasting Coating: The lifespan of the coating depends on the powder composition. High-durability polyester and polyurethane coatings last up to 5 years, while super-durable acrylic and fluoropolymer-based formulations can last over 30 years.
- Corrosion Resistance: The polymer film creates a barrier against corrosion, protecting metal surfaces exposed to harsh environments.
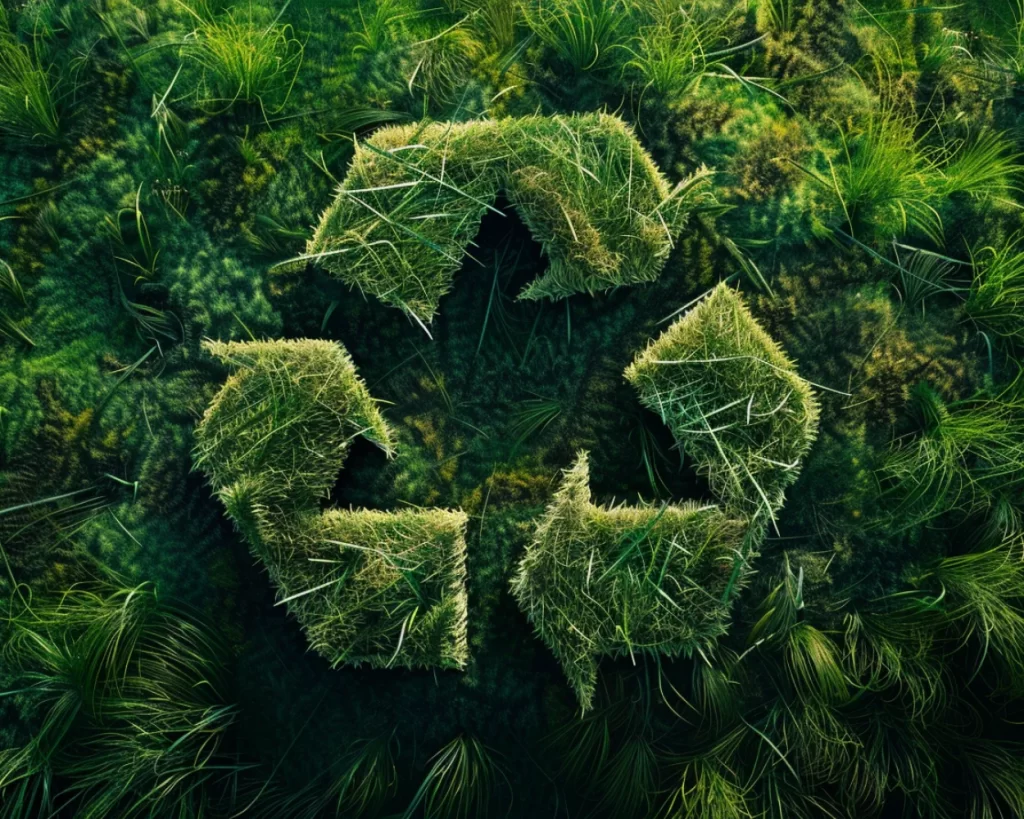
Environmental Safety
- No VOC Emissions: Powder coatings contain no solvents, so they do not emit volatile organic compounds (VOCs). VOCs can be harmful to human health, causing respiratory issues and potentially leading to cancer. Powder coatings help create safer environments for people and maintain environmental cleanliness.
- Minimal Waste: During application, about 60% of the powder adheres to the surface, while the excess remains in the spray booth. This excess can be collected and reused in a process called reclamation. As a result, manufacturers can utilize over 90% of the powder, minimizing production waste.
- Energy Efficiency: The curing process occurs at temperatures of 160-120°C for about 10 minutes, requiring minimal energy consumption from manufacturers.
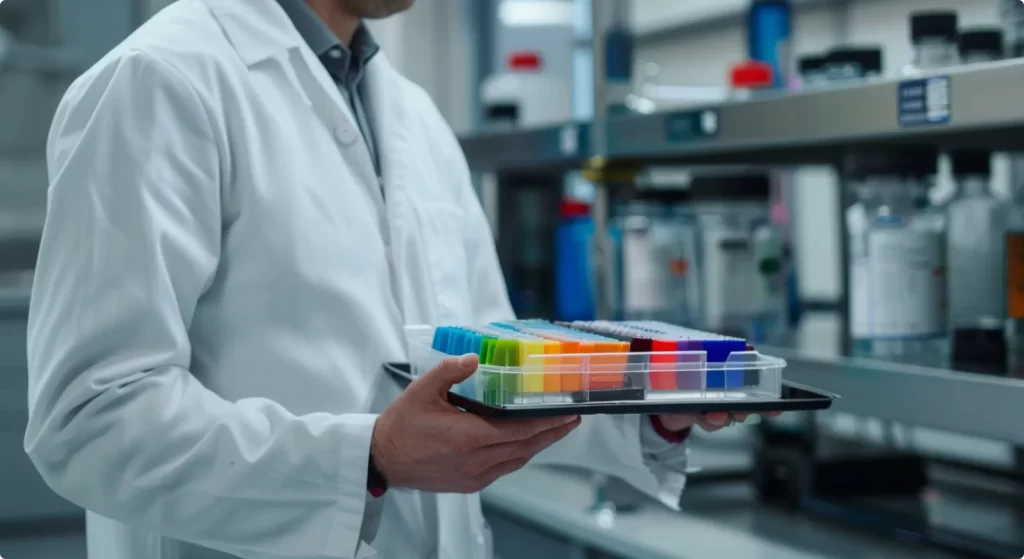
Economic Efficiency
- Reduced Operating Costs: The powder coating application process can be fully automated, reducing labor costs and production time.
- Lower Waste Management Costs: By using powder reclamation systems, up to 95% of the excess powder can be reused, reducing waste volumes and disposal costs.
- Long-Term Savings: The durability of powder coatings reduces the frequency of reapplications and maintenance. High-durability coatings can last up to 10 years without requiring repairs, which significantly lowers operational costs for industrial and infrastructure projects.
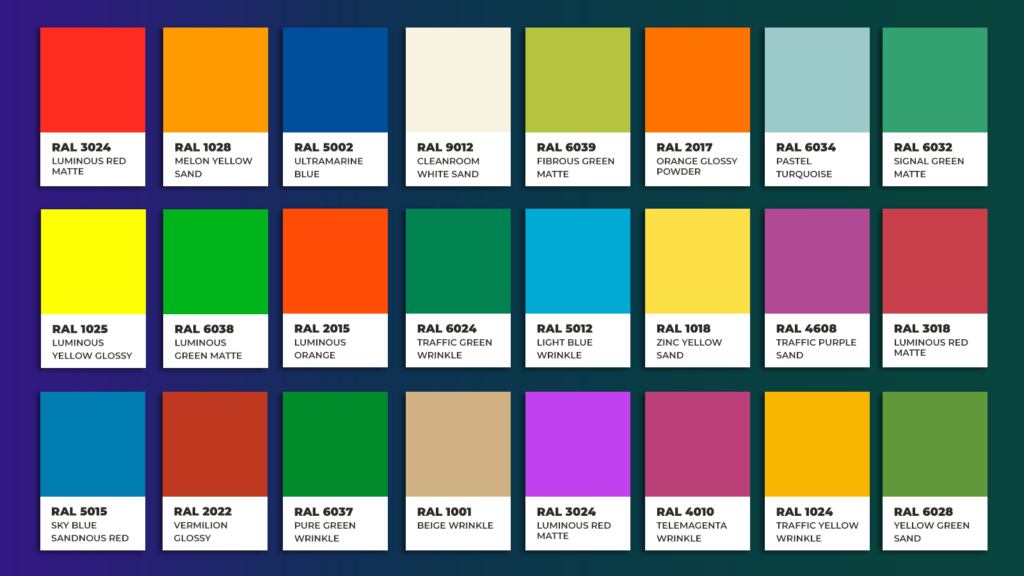
Aesthetic Flexibility
- Wide Range of Options: Includes glossy, matte, and textured finishes to meet diverse design requirements. Over 5000 colors and textures are available on the market, including special effects like metallic, chameleon, and antique. Manufacturers can also develop custom colors and textures for specific projects.
- Custom Color Matching: Powder coatings meet branding and design specifications. Color experts use spectrophotometers and computer color matching systems to create precise color formulations. The color matching accuracy can achieve Delta E<1, an imperceptible deviation from the standard to the human eye.
- Versatile Applications: The technology is suitable for industrial equipment, automotive parts, household appliances, and architectural elements. The use of powder coatings is growing annually by 4.5-7% in the automotive industry for wheel coatings, in construction for protecting metal structures, and in appliance manufacturing for coating washing machine and refrigerator bodies.
Types of Powder Coatings
Powder coatings contain standard components, including pigments for color, additives for light stabilization, and protection against photodegradation. The base of the powder is a resin, and the type of resin used determines the application possibilities and durability of the coating. Based on the type of resin, the following types of powder coatings are distinguished:
Applications
- Automotive wheels, bumpers, and decorative elements
- Aluminum profiles, window frames, and facades
- Outdoor furniture
- Playground equipment
- Agricultural machinery
- Lighting fixtures
- Garden tools
Applications
- Household appliances (washing machines, dryers, refrigerators)
- Office furniture
- Shelving and fixtures
- Electrical panels
- Lighting fixtures
- General industrial applications
Applications
- Pipelines and valves
- Oil and gas industry components
- Rebar and steel structures
- Electrical enclosures
- Automotive underbody components
- Metal furniture
Applications
- Automotive wheels and decorative elements
- Outdoor furniture
- Industrial equipment and machinery
- Household appliances
- Architectural elements
- Sporting goods and outdoor playground equipment
Finish Options
Powder coatings offer a variety of finish options to meet different aesthetic and functional requirements. The texture of the coating is as crucial as its color and, in some cases, can be even more important.
Smooth Finishes
Smooth finishes are achieved through careful formulation of the powder and precise control of the curing process. These finishes typically utilize fine particle size distributions (typically 20-50 μm) and flow additives like acrylates or silicones to promote leveling during the melt and flow stages of curing.
This finish can highlight surface imperfections in the substrate and may be more prone to showing scratches.
Advantages:
- Excellent surface uniformity
- High cleanability and ease of maintenance
- Optimal for applications requiring minimal friction or drag
Textured Finishes
Textured finishes are created by incorporating specific additives or by manipulating the powder formulation and curing process. Texturing agents such as silicon dioxide, polytetrafluoroethylene (PTFE), or specialized polymers are often used to create surface irregularities.
Textured powder coating can be more challenging to clean thoroughly and may trap contaminants in high-wear applications.
Advantages:
- Masks minor substrate imperfections
- Provides improved grip and slip resistance
- Generally more resistant to scratches and wear
Glossy finishes are achieved through the use of resins with high flow characteristics and careful control of the curing process. Epoxy and polyester resins are commonly used, often with flow modifiers to enhance surface leveling.
Textured powder coating can be more challenging to clean thoroughly and may trap contaminants in high-wear applications.
Glossy finish may create glare in certain lighting conditions.
Advantages:
- High aesthetic appeal with a reflective surface
- Excellent cleanability and chemical resistance
- Good for applications requiring high visibility or light reflection
Matte finishes are created by incorporating matting agents such as silica or by using resins with inherently lower gloss characteristics. The surface roughness is controlled at a microscopic level to diffuse light reflection.
Over time, it can appear burnishing or polishing in high-wear areas.
Advantages:
- Reduces glare and reflections
- Hides minor surface imperfections and scratches
- Provides a sophisticated, modern appearance
Color Variety
Powder coatings offer a wide range of color options to meet diverse aesthetic and functional needs. The two primary approaches to achieving the desired color in powder coatings are using standard color palettes and custom color matching.
Standard color palettes in the powder coating industry are pre-formulated sets of colors that manufacturers offer as readily available options. These palettes typically include a range of common colors and finishes that cater to a broad spectrum of applications and customer preferences.
Standard color palettes are particularly well-suited for:
- High-volume production: When large quantities of coated products are needed in consistent colors.
- Quick turnaround projects: Where time constraints preclude custom color development.
- Cost-effective solutions: Standard colors are often more economical due to economies of scale in production.
- Maintenance and repair: For touch-ups or replacements where matching existing colors is crucial.
Advantages for Customers
Glossy finishes are achieved through the use of resins with high flow characteristics and careful control of the curing process. Epoxy and polyester resins are commonly used, often with flow modifiers to enhance surface leveling.
Textured powder coating can be more challenging to clean thoroughly and may trap contaminants in high-wear applications.
Glossy finish may create glare in certain lighting conditions.
- Immediate availability: Standard colors can often be ordered and shipped without delay.
- Consistent quality: These colors have been thoroughly tested and optimized for performance.
- Lower minimum order quantities: Customers can often purchase smaller amounts compared to custom colors.
- Easier specification: Standard colors simplify the process of specifying coatings across multiple projects or suppliers.
Industry Use
In the powder coating sector, we rely on several standardized color systems to ensure consistency and ease of specification. The three primary systems are work here:
RAL System
The RAL system is the most widely used color standard in the powder coating industry, particularly in Europe. It comprises several collections:
- RAL Classic: Contains 213 colors, each designated by a four-digit code. For instance, RAL 9010 is Pure White, while RAL 3020 is Traffic Red.
- RAL Design: An expanded system with 1,625 colors, using a seven-digit code based on hue, lightness, and chroma.
- RAL Effect: Includes 420 solid colors and 70 metallic colors, focusing on more contemporary hues.
In powder coating formulation, RAL standards are used as precise color targets, often measuring coatings’ color using spectrophotometers to ensure a Delta E value (color difference) of less than 1.0 from the RAL standard.
Pantone System
While primarily developed for the printing industry, the Pantone Matching System (PMS) has found significant use in powder coatings, especially for brand color matching. Key aspects include:
- Pantone Solid Coated: Most relevant for powder coatings, as it represents colors on a glossy surface.
- Color communication: Pantone codes are often used in client specifications, requiring to develop close matches in powder form.
NCS System
The Natural Color System (NCS) is less commonly used in powder coatings but is gaining traction, especially in architectural applications. Its features include:
- Perceptual basis: Based on how humans perceive color, using six elementary colors (white, black, yellow, red, blue, green).
- Notation system: Describes colors by their visual properties rather than pigment mixtures.
- Conversion capability: The manufacturer can convert NCS notations to powder formulations, using the spectrophotometric analysis and custom mixing.
Custom Color Matching
In addition to these standardized systems, powder coating manufacturers develop proprietary color collections. These typically include:
- Industry-specific palettes: Tailored color ranges for sectors like automotive, appliances, or architectural applications.
- Effect collections: Specialized finishes such as metallic, textured, or color-shifting powders that go beyond solid colors.
- Trend-based collections: Curated color ranges that align with current design trends and forecasts.
When formulating powder coatings to match these color standards, the developer must account for various factors such as the resin system (e.g., polyester, epoxy, or hybrid), pigment stability, and curing conditions. The goal is to achieve not just a visual match, but also to ensure color stability under UV exposure and various environmental conditions.
Product Development
- Receive a powder coating designed specifically for your production within 2-4 business days.
- Shorten the time required to launch a new product or color offering.
Applications of Powder Coating
Powder coating is versatile and can be applied across various industries due to its durability, efficiency, and environmental benefits.
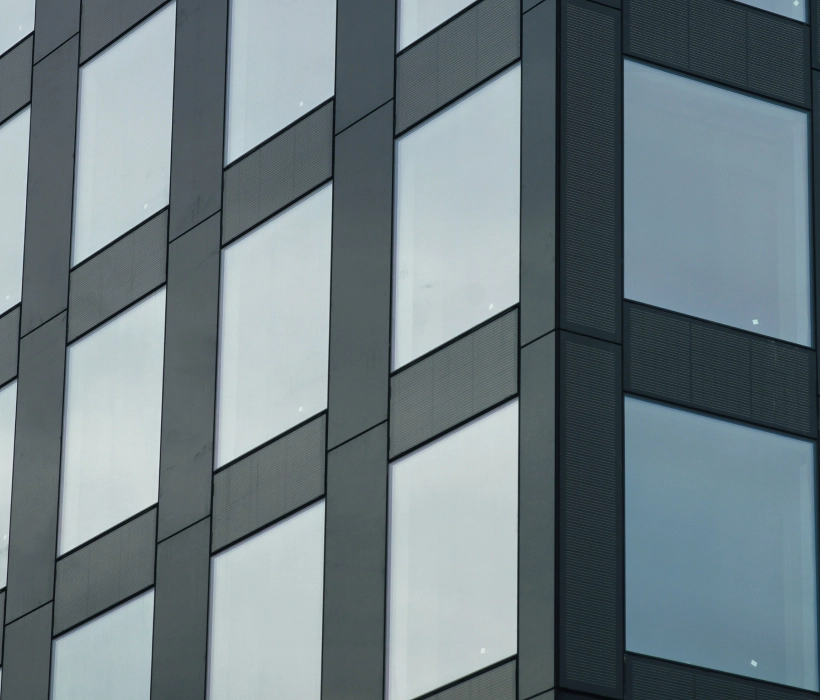
Items: Aluminum window frames, metal facades, railings, light poles, fencing, garage doors, and HVAC equipment.
Functions: Weather resistance, UV protection, corrosion resistance, and aesthetic appeal.
Development opportunities: Improvements in heat-reflective coatings for energy efficiency, self-cleaning surfaces, and integration with smart building technologies.
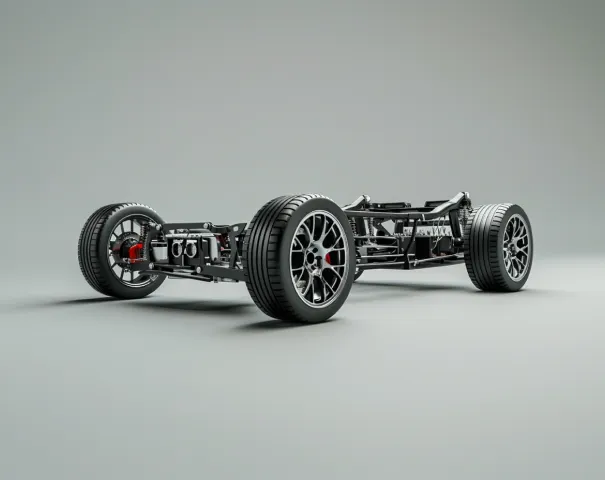
Items: Wheels, bumpers, chassis components, engine parts, door handles, roof racks, and underbody components. In mass transit, entire bus and train exteriors.
Functions: Corrosion protection, chip resistance, and aesthetic finishing for both interior and exterior components.
Development opportunities: Ultra-low-cure formulations for heat-sensitive substrates, improved metallic finishes, and coatings compatible with lightweight materials like carbon fiber composites.
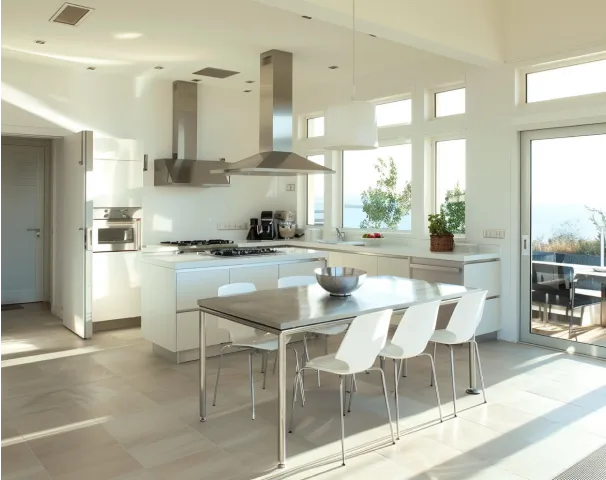
Items: Metal office chairs, filing cabinets, shelving units, table legs, bed frames, outdoor patio furniture, and metal school furniture.
Functions: Aesthetics, durability, and resistance to daily wear and tear.
Development opportunities: Antimicrobial coatings, improved texture options, and coatings with enhanced chemical resistance for commercial furniture.
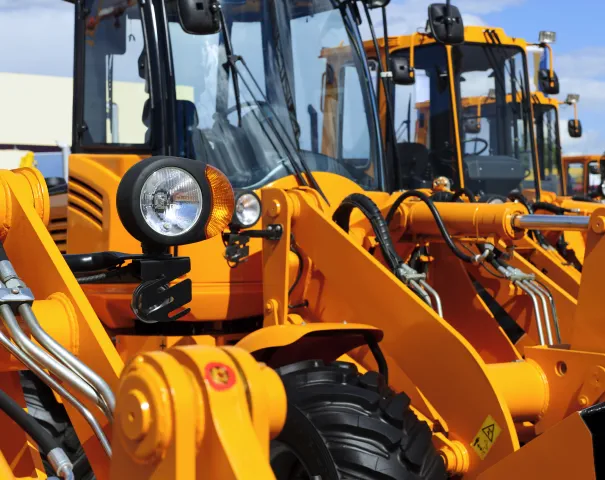
Items: Tractor bodies and components, combine harvester parts, bulldozer frames, excavator arms, forklift bodies, and scaffolding equipment.
Functions: Corrosion and chemical resistance, UV stability, and high durability in harsh environments.
Development opportunities: Self-healing coatings, improved adhesion to complex substrates, and coatings with enhanced abrasion resistance.
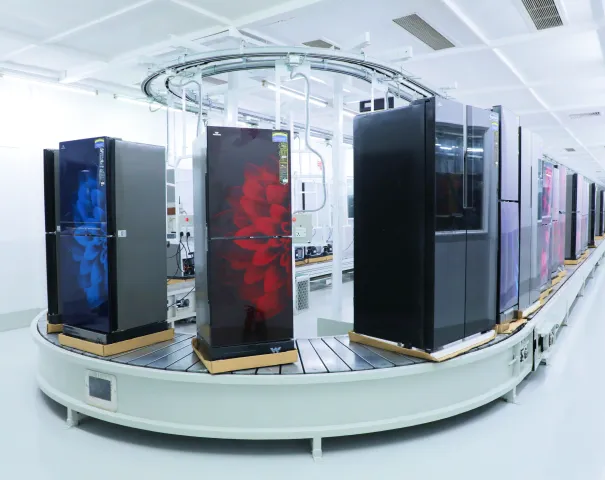
Items: Refrigerator exteriors, washing machine drums, dryer bodies, microwave oven interiors, dishwasher racks, stove components, and water heater tanks.
Functions: Aesthetic finish, chemical resistance, and durability against frequent use.
Development opportunities: Energy-curable systems for heat-sensitive components, fingerprint-resistant finishes, and improved anti-microbial properties.
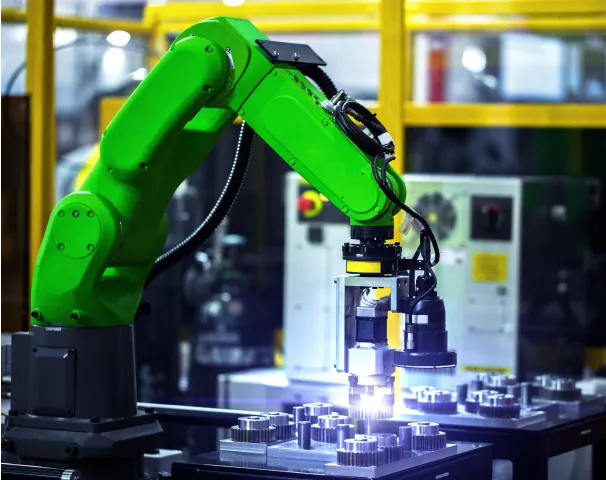
Items: Pipe fittings, valves, pumps, compressors, electrical enclosures, machine tools, conveyor systems, and industrial fans.
Functions: Corrosion protection, chemical resistance, and specific performance attributes based on the application.
Development opportunities: Faster curing systems, improved edge coverage, and coatings with enhanced functional properties like electrical insulation or thermal management.
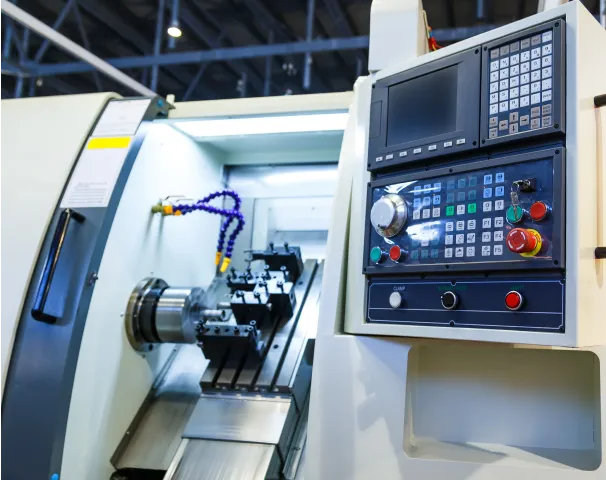
Items: Electrical insulators, transformer components, heat sinks, friction-reducing coatings on industrial rollers, and chemical-resistant coatings on laboratory equipment.
Functions: Electrical insulation, thermal management, friction reduction, and chemical resistance.
Development opportunities: Nano-engineered coatings for enhanced properties, conductive coatings for EMI/RFI shielding, and coatings with improved tribological properties.
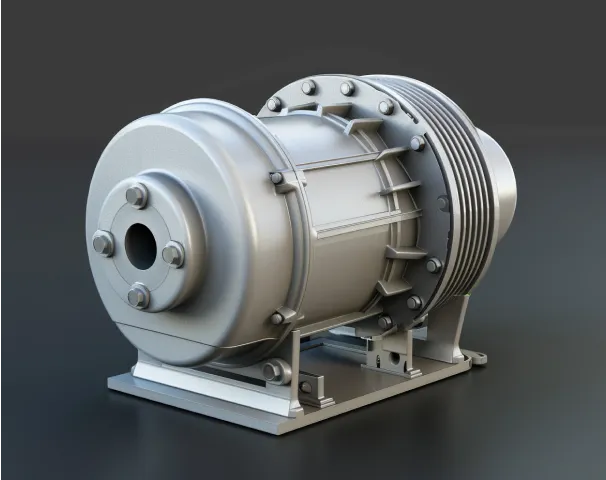
Items: Electric motor housings, battery casings, charging station components, electrical switchgear, and power distribution equipment.
Functions: Electrical insulation, thermal management, and protection against environmental factors.
Development opportunities: Coatings with improved dielectric strength, thermal conductivity for better heat dissipation, and formulations compatible with new battery technologies.
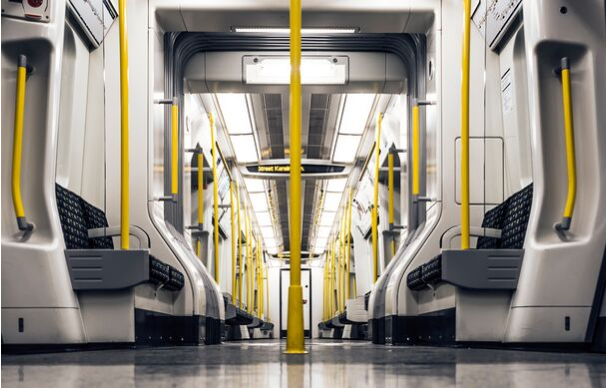
Items: Garden tools, bicycle frames, exercise equipment, lamp bases, picture frames, coat hangers, bathroom fixtures, and kitchen utensils.
Functions: Aesthetic appeal, durability, and resistance to household chemicals.
Development opportunities: Expanded color and texture options, coatings with improved tactile properties, and environmentally friendly formulations appealing to eco-conscious consumers.
How to Choose Powder Coating
To make the right choice, follow these tips.
For Manufacturing (Commercial Use)
- Substrate Material. Consider the base material you're coating. Different substrates (e.g., steel, aluminum) require specific powder formulations for optimal adhesion and performance. For metals, ensure proper pre-treatment (e.g., phosphating, chromating) to enhance adhesion and corrosion resistance.
- Environmental Exposure. Assess the environment where the coated product will be used. For outdoor applications, choose super-durable polyester systems with enhanced UV resistance.
- Aesthetic Considerations. Factor in color, gloss level, and texture requirements. Remember that some effect finishes (e.g., metallic) may require special application techniques. For color-critical applications, always conduct physical sample approvals under intended lighting conditions.
- Regulatory Compliance. Ensure the chosen powder meets relevant industry standards and regulations (e.g., AAMA, Qualicoat, GSB) for your specific application.
- Application Method. Consider your application equipment and process. Some powders are optimized for specific application methods (e.g., tribo or corona charging). For complex geometries with Faraday cage areas, consider powders with enhanced penetration properties or specific application techniques.
- Cure Schedule: Match the powder's cure requirements with your production line capabilities. Low-temperature cure systems can be beneficial for heat-sensitive substrates or energy savings. Always verify complete cure using solvent rub tests or differential scanning calorimetry (DSC) analysis.
For DIY Applications
- Equipment Compatibility. Ensure the powder is compatible with your application equipment. Most DIY setups use corona charging guns. Look for powders with a wide application window to accommodate variations in application technique.
- Cure Temperature. Verify that your curing setup (often a kitchen oven) can reach and maintain the required cure temperature. For DIY applications, consider powders with lower cure temperatures (around 180°C). For example, the glossy polyester powder coating paints cured at 160 °C. The cure temperature around 160-180 also suits epoxy-polyester and epoxy coatings.
- Surface Preparation. Emphasize thorough cleaning and proper pre-treatment. For DIY, phosphate-free metal preparations are often more suitable. Always degrease surfaces and consider using a conversion coating spray for enhanced adhesion.
- Powder Quantity. Purchase appropriate quantities. Unlike liquid paints, powder coatings can't be easily mixed for small batches. Look for suppliers offering small quantity packages suitable for DIY projects.
- Ease of Application. For beginners, start with powders known for good flow and leveling properties to achieve a smooth finish more easily. It suits polyester and epoxy-polyester coatings with smooth texture. Practice on scrap pieces to get a feel for the powder's behavior before coating your final product.
The Powder Coating Process - Step-By-Step Guide
- Inspect the part for defects or contaminants.
- Clean the substrate thoroughly to remove oils, greases, and other contaminants.
- For metals, use appropriate solvents or alkaline cleaners.
- For non-conductive substrates, consider using a conductive primer.
- Apply chemical pre-treatment to enhance adhesion and corrosion resistance.
- For ferrous metals, use iron or zinc phosphate conversion coatings.
- For aluminum, use chromate or chrome-free conversion coatings.
- Rinse thoroughly with deionized water to remove residual chemicals.
- Dry the part completely to prevent moisture-related defects.
- Use forced air or an oven set at 100-120°C.
- Ensure no water droplets remain, especially in recessed areas.
- Apply high-temperature resistant tapes or plugs to areas that should not be coated.
- Ensure masks are securely attached to prevent powder ingress.
- Ground the part properly to ensure electrostatic attraction.
- For manual application, maintain a distance of 6-8 inches (15 - 20 sm) from the part.
- For automatic systems, optimize gun settings (voltage, current, air pressure) based on powder type and part geometry.
- Apply powder uniformly, targeting a film thickness of 60-80 microns for most applications.Use spray systems that have built-in thickness estimators based on powder flow rates and coverage area.
- Transfer the coated part to the curing oven promptly to avoid contamination.
- Set oven temperature and time according to the powder's technical data sheet.
- Typical cure schedules range from 10 minutes to 30 minutes at 160-200°C.
- Use data loggers or temperature indicators to ensure the part reaches full cure temperature.
- For large or thick parts, allow additional time for the substrate to reach cure temperature.
- Allow parts to cool naturally to room temperature.
- Avoid rapid cooling to prevent thermal shock and potential coating defects.
- Visually inspect the coating for defects like orange peel, pinholes, or insufficient coverage.
- Measure film thickness using non-destructive methods (e.g., magnetic or eddy current gauges).
- Perform a solvent rub test to verify complete cure.
- For minor defects, use specialized powder touch-up materials.
- For major defects, strip the coating completely and restart the process.
- Conduct final appearance and performance checks.
- Verify color and gloss levels match specifications.
- For functional coatings, perform relevant tests (e.g., electrical resistance for insulating coatings).
- Allow coated parts to fully cool before packaging.
- Use appropriate packaging materials to prevent damage during transport.
- Maintain a clean environment throughout the process to avoid contamination.
- Regularly calibrate and maintain all equipment for consistent results.
- Monitor environmental conditions (temperature, humidity) as they can affect powder application and cure.
- For new applications, always conduct trials to optimize process parameters.
- Keep detailed records of process conditions for traceability and continuous improvement.